Flash and
Reprogramming Support
CAN/CAN FD tool
NETIMPRESS air
For development, production, and maintenance of in-vehicle Small-sized and lightweight CAN reprogramming tool Also includes CAN test and logger functions for the field
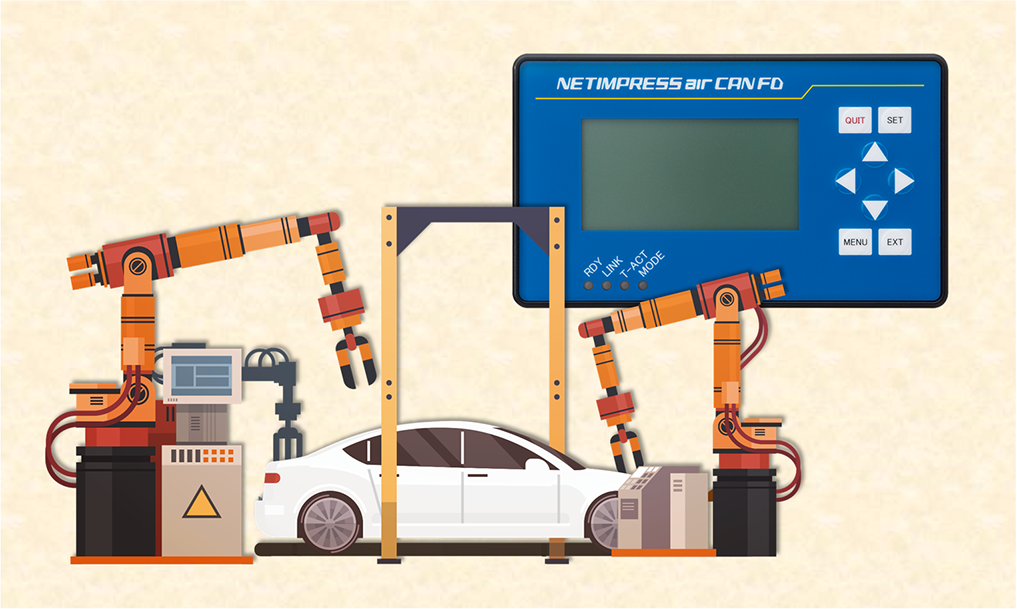
Small-sized and lightweight CAN/CAN FD tool to support software updates for the field:
NETIMPRESS air
Our NETIMPRESS series has a proven track record of flash programming support developed over many years of experience. Our company also provides reprogramming based on CAN communication to many automotive customers. NETIMPRESS air is a tool specializing in flash reprogramming for in-vehicle ECU development sites, and has been made into a small-sized and lightweight model with priority given to ease of use on site.
It also comes with CAN communication monitor & log and pseudo CAN transmission test functions that can be used in the reprogramming peripheral environment, so it can also be used to check software update status.
Product features
- We have condensed the know-how specialized in reprogramming cultivated over many years of experience into on-site tool specifications.
- Three solutions for a wide range of applications: reprogramming/bus monitor logging/CAN testing
- Compact size with excellent portability for ECU development and evaluation sites.
- No need for AC power supply suitable for actual machine environment: Use target power supply (12V) or USB power supply
- Supports CAN 2.0B (Max: 1Mbps) and CAN FD (Max: 8Mbps) as communication standards
- Depending on the PC-less environment at the site, stand-alone operation is possible by utilizing the on-board SD card
- For remote evaluation equipment, WLAN-equipped models also support PC operation via wireless communication
Reprogramming solutions for a variety of applications
NETIMPRESS air is expected to be used for reprogramming in a wide range of sites.
- ECU flash reprogramming work for vehicle test development at automotive OEM
- ECU stand-alone reprogramming prior to implementation in vehicles as a production site support
- Wireless reprogramming for EOL (End-of-Line) of assembly processes on production lines
- Reprogramming support for ECU development verification and evaluation at automotive parts suppliers
- Software update support and field tools for maintenance of control products equipped with CAN communication.
※We have a free version of the programmer control PC software "NETIMPRESS air Connect" that has the same operating environment as the conventional NETIMPRESS series. (Download from dedicated website).
ECU test solution (CAN scenario transmission)
NETIMPRESS air has a function that registers transmission information in a scenario file as a pseudo CAN node for ECU development and production inspections, and automatically transmits data messages registered in the file at a set timing.
The information that can be registered in the scenario file is script information that defines sending messages, sending timing specifications, repeated sending, single sending, etc
Activation of the scenario transmission function can be performed remotely from the HOST-PC or by external command timing.
<As a reference example>
When the ECU connected to the in-vehicle network of a completed vehicle is turned on (ignition power is turned on), a CAN message for initialization and synchronization is sent from a specific ECU to each ECU.
In the ECU unit test, we will introduce an example where NETIMPRSS air emulates the CAN message initialization operation at IG-ON instead of the ECU.
Logging solution
It is possible to monitor and log frame data of the CAN/CAN FD communication bus connected to NETIMPRESS air. The monitor & log function includes functions such as monitoring the status of CAN communication with a real-time bus monitor, and starting and ending logging based on trigger conditions. The recorded log data can be saved to a CSV file.
By observing the CAN bus under specific conditions, it is expected to be useful for capturing changes in ECU operation, understanding abnormal operation phenomena, and identifying causes.
With NETIMPRESS air, you can use it as a handy tool at your local work site, recording changes in CAN communication status before and after reprogramming, and using scenario transmission to check operation.
※A free version of "NETIMPRESS air Logger" is available as software for logger control and observation. (Download from dedicated website)
NETIMPRESS air product specifications
The product specifications of NETIMPRESS air are introduced below.
●Body (AF932)
Two types of main units are available: a standard model (AF932) and a WLAN-equipped model (AF932/W).
【Display LED, operation SW and connector】
<Front Panel>
・LCD (displays information such as defined type name and address display)
・Key (operation key for standalone)
・LED (displays various air status)
<Upper side> Target Connector
<Lower side> SD Card Slot (dedicated SD card slot)
Tool cooperation trigger/USB connector (with cover)
【Basic specifications】
・Target interface:
CAN/CAN FD 2ch (Communication speed: 125Kbps to 8Mbps)
K-LINE 1ch (input allowable voltage V-BAT ±0.5V)
User power supply (V-BAT) Allowable voltage range 8~16V
Trigger input 1ch
・Host interface:
USB2.0 High Speed (mini-B), Wireless LAN (/W)
WLAN IEEE 802.11b/g/n (2.4GHz)
・Operating temperature -20~45℃ (normal), -20~65℃ (CAN operation)
・External dimensions 133(W)×78(D)×37(H)mm
・Weight approx. 240g
・Power supply VBAT DC8~16V, USB 5V±5%
・Power consumption: 5W or less when powered by VBAT, 2.5W or less when powered by USB,
30mA or less in low power mode (VBAT power supply)
●Accessories (sold separately)
Target connection probe
AZ915:
High Speed CAN probe 1m (IF-CN : D-sub 9 pin)
AZ916:
High Speed CAN probe 1m(IF-CN : Untreated ends)
Trigger cable(Coaxial Cable Assembly )
AZ905: MMCX connector on both end
AZ906: MMCX connector to Alligator Clip Cable
●Dedicated SD card (FX900)
This is a dedicated SD card for AF932 products.
It supports memory sizes up to 32GB.Programming environment data is saved in the YIM folder as with previous products. By utilizing programming, it is possible to change to the next target microcontroller by instantly switching the YIM folder.
●License (Definition License)
①CAN/CAN FD programmer function
②CAN/CAN FD logger function
③CAN/CAN FD test function (custom)
The above licenses are available and you can choose according to your needs. In addition, additional functions and new features that will be expanded in the future can be used by adding licenses.
Due to improvements in performance, quality, etc., the contents may be changed without notice.