Gasoline Engine System
【Real-Time Target System Verification of Engine Management System ECU:Real-time Variable Measurement of Management System ECU Software under Real-Time Target System Environment(Comparison with CAN tools)】
Variable measurement with 100 times finer granularity than CAN tools
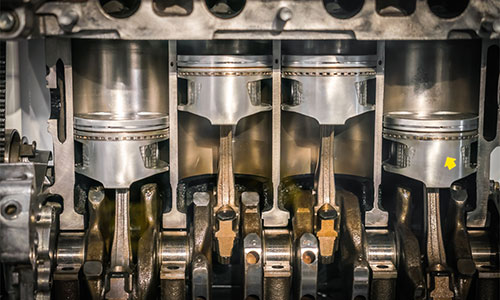
The engine management system ECU instantly controls fuel injection and ignition timing in synchronization with the opening and closing of the throttle and RPM.Fuel injection and ignition timing control requires settings to “maximize torque,” “optimize air/fuel mixing,” and “reduce toxic emissions.
The control algorithm performs optimal control each time based on the sensor input of each state and calculations necessary for ignition timing and fuel injection control (air-fuel ratio, knock, torque, rotation speed, vehicle speed, exhaust gas).
Above is an image of a 4-stroke, 4-cylinder direct-injection engine.In the 4-stroke process of a 4-cycle, one process (intake, compression, combustion, and exhaust) is defined as two crank revolutions (720 degrees).One process at 8000 rpm is about 15 msec.
By measuring the behavior of internal variables of the control MCU implemented in the ECU, the validity of the engine control process can be verified.In the case of measuring internal variables via CAN communication, the variable measurement possible in one process (720 degrees) at 8000 rpm is about 16 variables (32 bits).RAMScope can measure the same level of variables in one-shot (10-degree) increments of the crank angle without a resident program for verification.With one process, it is possible to measure more than 1,000 variables, enabling verification of detailed control processes.