Multi-Axis Motor Control
RAMScope is ideal for verifying the operation of cooperative control with MCUs for high-performance multi-axis motors!
(Renesas Electronics RX66T/72T Support Introduction)
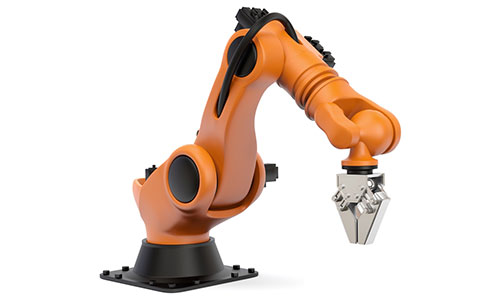
【Supports Renesas Electronics' RX66T and RX72T specialized for multi-axis motor control】
The RX66T/RX72T from Renesas Electronics' it is possible to control up to four motors simultaneously.They also feature high-resolution PWM (Pulse Width Modulation) for fine-tuned inverter control, and offer high performance for industrial applications.Controlling up to four motors with a single core is very powerful for multi-axis motor control.
Multi-axis motor control requires highly accurate position and velocity control as a system, and requires cooperative control in which each axis interpolates with each other.Multi-axis cooperative control systems require multiple motors, so they need to be smaller and lighter.Therefore, a servo-controlled model with brushless DC motors is has been adopted, which enables miniaturization.Although downsizing the motor increases the current ripple, the current ripple can be reduced by increasing the switching frequency of the PWM control to the inverter.
The RX66T/RX72T can generate PWM carrier frequency from the CPU operating frequency (160MHz/200MHz), which is expected to reduce current ripple.Highly efficient power management with built-in high-resolution PWM enables fine-tuned drive control to the inverter.Vector control is often used in motor control.
【RAMScope is the best choice for “MCUs for multi-axis motors” and “operation verification of cooperative control】
Vector control is an independent control of the currents that generate torque and magnetic flux.In actual control, the motor drive phase currents are monitored, the spatial coordinates of the current and magnetic field axes are obtained, and three-phase drive currents (PWM register settings) are generated according to PI control.
RAMScope's measurement application allows independent graphical display of the internal variables of vector control operations (motor phase currents, dq-axis currents, PI parameters, PWM register settings, etc.) for each axis.It is also possible to overlay internal variables of different control axes, making it possible to "visualize" the correlation state.The figure above shows an example of the torque command value, PWM register settings, and phase current measurements for each motor shaft according to the motor control cycle.It has an extensive track record as a measurement tool in cooperative control systems for the automotive applications, and is also an ideal tool for multi-axis motor control applications.